Our Stop’n Go service model for power plant maintenance outages save you nerves, time and money
Stop n’ Go Smart Blasting
Additional services
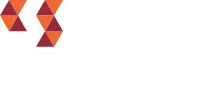
Simplifying maintenance outages
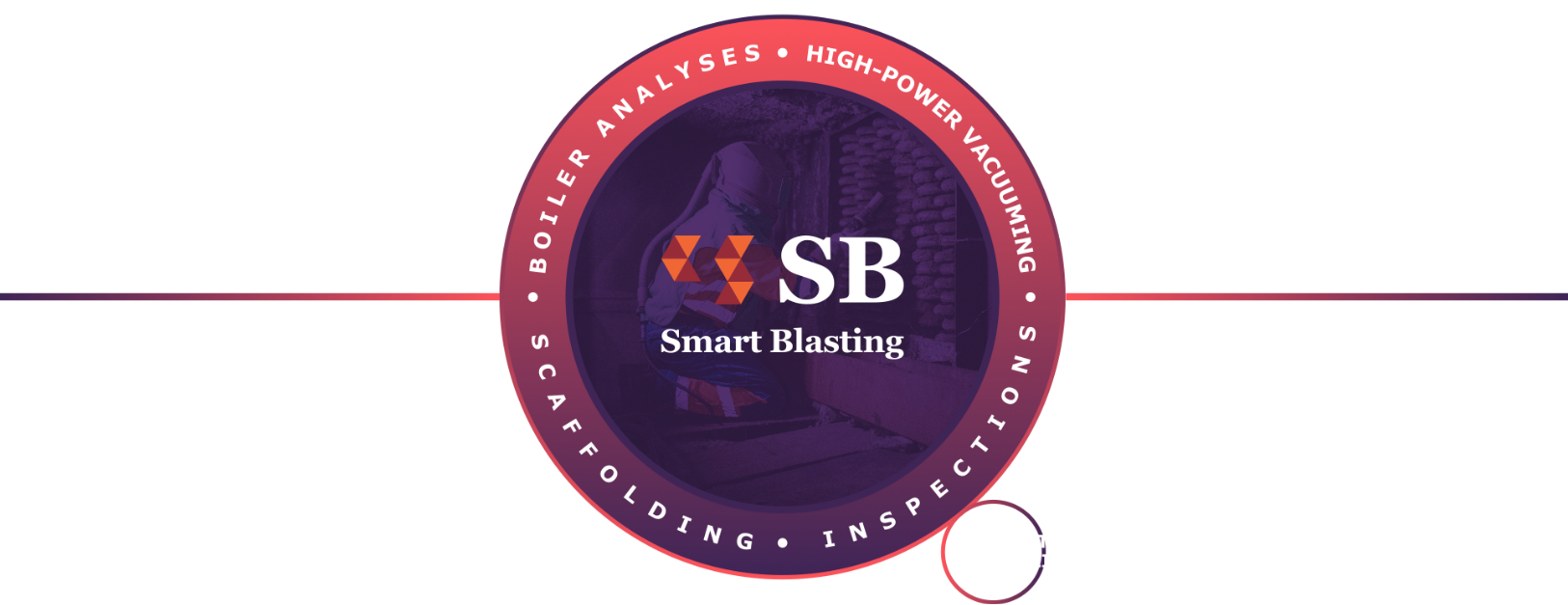
Phase 1
Planning
- Our projects always start with a clear plan
- This plan is made with our customer to match their schedules
- It includes a detailed workflow of the tasks to do and how much time each takes
- The plan is shared with the project team and customer
- Every project has a dedicated project manager
- Our project manager is responsible for project schedules and outcome
Phase 2
Maintenance outage
The Stop’ n Go service model can include the following tasks
- Cleaning the boiler’s heat transfer surfaces with our patented Smart Blasting ™ method
- Vacuuming and disposing of cleaning waste and any additional vacuuming services (CS vacuuming)
- Boiler NDT inspection (CS Check)
- Scaffolding work
- We can optimise resources and costs by offering a broader scope of work to make your life easier
Phase 3
Reports
- Our projects are always finalised with a written project report and photos
- The report includes a document of work performed and observations
- We always give our recommendations for the next outage
- This report is delivered to our customer within two weeks after the maintenance outage is completed
Choose us.
We help our customers to see the benefits of clean heat transfer surfaces as a significant factor in maintaining a profitable business.